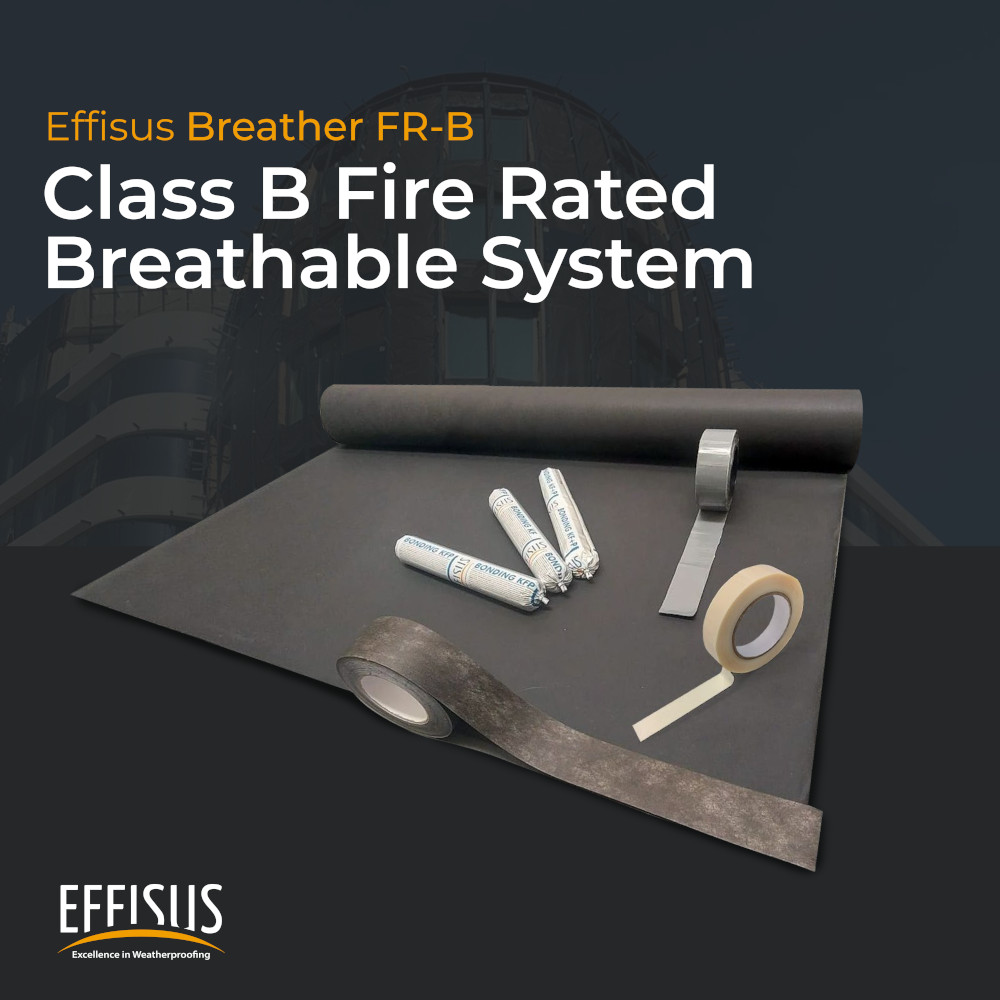
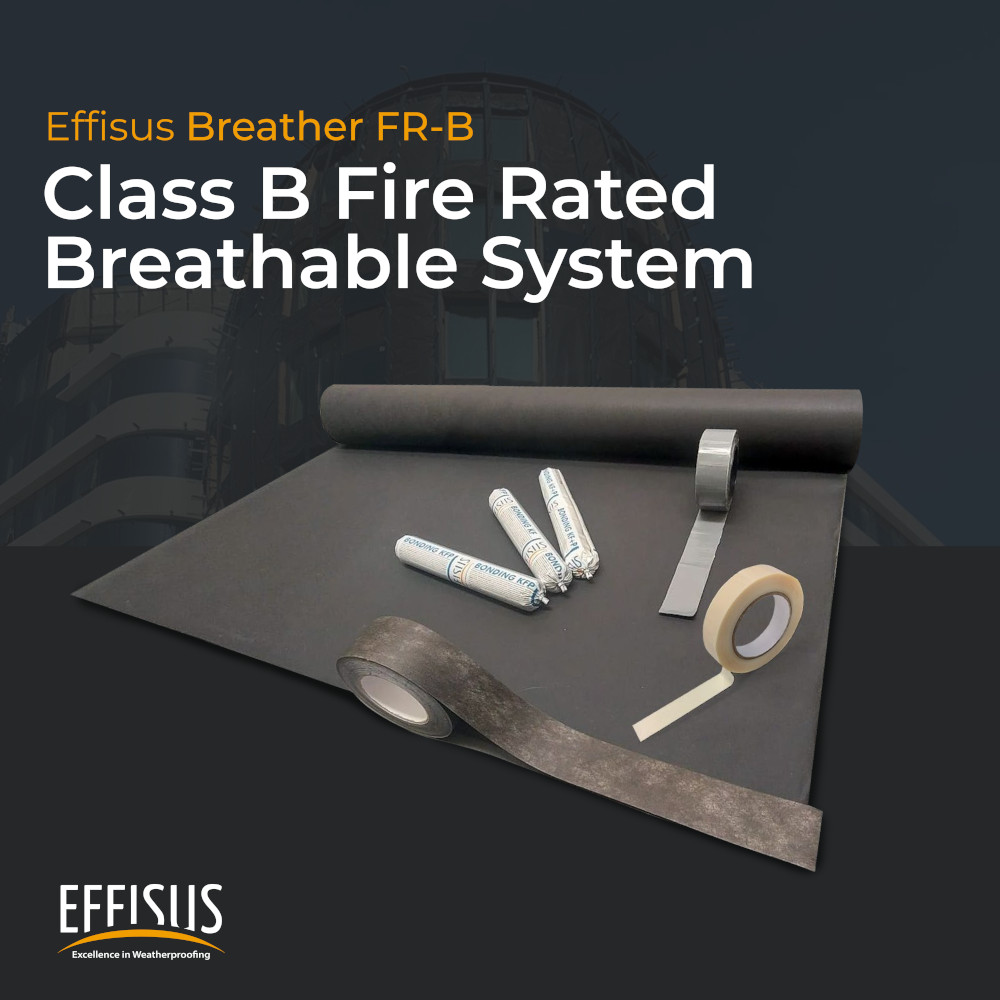
In the construction industry today, ensuring building durability, energy efficiency, and protection from environmental factors is of utmost importance. As building technologies advance, so do the solutions available to architects, engineers, and contractors aiming to create sustainable, safe, and durable structures. Building facade protection plays a critical role in achieving these objectives. From high-performance insulation to fire rated facade membranes, these innovations are essential for protecting buildings and improving their energy efficiency. This guide explores key building facade solutions leading to the ultimate product recommendation for comprehensive building envelope protection. Building facade protection and high-performance insulation The outer shell…
In the construction industry, ensuring the safety and durability of buildings is of utmost importance. One critical aspect of building protection is fire safety. Fire rated membranes are essential components that enhance the fire resistance of building facades, providing a crucial layer of defense against potential fire hazards. For more information on related building solutions, check out our previous article: What are Facade Solutions for High-Performance Insulation. Understanding fire rated membranes Fire rated membranes are specially designed materials used to enhance the fire resistance of building envelopes. These membranes act as a barrier to resist ignition and slow the…
In the ever-evolving world of construction, ensuring the longevity and durability of buildings is paramount. One of the most critical aspects of building protection is safeguarding against the elements. This is where weatherproofing facade membranes come into play. A weatherproof membrane acts as a barrier, protecting buildings from environmental challenges. By implementing a weatherproof membrane system, structures are better equipped to handle external stressors, ensuring they remain resilient and energy-efficient over time. The right weatherproof membrane can significantly reduce maintenance costs and extend the building’s lifespan, making it an essential choice in modern construction. For more information on related building…
In modern construction, the emphasis on sustainability, energy efficiency, and longevity has never been more critical. High-performance insulation in facade solutions plays a crucial role in achieving these goals. There are various facade solutions designed to provide high-performance insulation, ensuring buildings are energy-efficient, durable, and environmentally friendly. The role of facade solutions Facade solutions encompass a range of products and techniques designed to enhance the performance of building envelopes. These solutions are integral to achieving high-performance insulation, as they form the outer shell of the building, protecting it from external elements while ensuring energy efficiency. Key components of facade…